Industry Tests Find No Free-standing Nanotubes Released from Tyre Wear
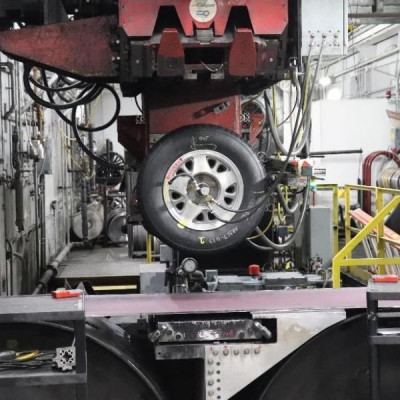
Tyre wear and brake dust particles now create more pollution in most cities than emissions. However, concerns have arisen about the issues those wear particles might create.
UK-based Emissions Analytics state that their investigation shows that the microscopic particles from tyre wear can be airborne and most end up being deposited at the roadside, if not on the road. Being airborne, there is potentially a risk to the environment, and to people.
At the Akron Rubber Development Laboratory (ARDL), a tyre with a tread enhanced with single wall carbon nanotubes was exposed to accelerated wear and handling simulation tests.
Analysis of captured airborne particles showed no free-standing nanotubes, and no aerosolised nanotubes were found in the air during simulation of the life cycle of tyres. This potentially unlocks the door to mass use of single wall carbon nanotubes that have tyre industry-acknowledged benefits: improved safety and durability, and reduced energy consumption and vehicle CO2 emissions.
Single-wall carbon nanotubes, also known as graphene nanotubes, offer unique benefits in comparison to standard tyre additives, such as silica and carbon black, leading to a growing number of projects for developing safer and more eco-friendly tyres. Possible release of nanoparticles into the air was of interest for the tyre industry, which is heavily focused on environmental aspects. OCSiAl, the world’s largest producer of single wall carbon nanotubes, took a lead in initiating wear simulation tests of a tyre enhanced with nanotubes.
The test was performed by ARDL at a Calspan facility in Cleveland, OH. “We have introduced TUBALL nanotubes produced by OCSiAl into tread to check the probability of nanoparticles exposure, as this tyre component experiences the main wear during the car’s motion. An independent laboratory captured any possible aerosol released and applied a specific quantification method relying on Raman spectroscopy for the detection of airborne particles. Only rubber particles with nanotubes embedded into the matrix were discovered. No free-standing TUBALL nanotubes were observed,” said Gunther Van Kerckhove, H&S Lead Manager at OCSiAl.
The performed test verifies the results shown by VITO, a leading independent European research and technology organisation, in 2017 during abrader tests on single-wall carbon nanotube-enhanced epoxy, polyethylene, and elastomer samples. Taber abrading tests revealed no free-standing or protruding nanotubes in those tests. The reason lies in single wall carbon nanotubes’ bonding strength and their unique morphology: ultra-flexible with a 3000:1 length-to-diameter ratio.
“Exposure monitoring studies with material samples are not sufficient for the tyre industry. We wanted to check the exposure of a real tyre with nanotubes during wear similar road conditions – to check the potential impact on human health and the environment. After confirming that no single wall carbon nanotubes are expelled during tyre usage, the next step will be to verify that there is no exposure during recycling of a tyre either,” said Jean-Nicolas Helt, Development and Support Leader for Elastomers at OCSiAl.
Single wall carbon nanotubes are currently the only market solution allowing the industry to achieve a long-awaited breakthrough in tyres: improved durability and safety on the road and reduced energy consumption, leading to cost savings and lower CO2 emissions to the environment.
Read the original article on Tyre and Rubber Recycling.